304 vs 409 stainless steel
304 stainless steel contains higher chromium and nickel, providing excellent corrosion and heat resistance. It is versatile and widely used in diverse applications, including food processing. On the other hand,
409 stainless steel has higher carbon content and lower chromium and nickel levels, offering good heat resistance and moderate corrosion resistance. Its cost-effectiveness makes it a popular choice for automotive exhaust systems.
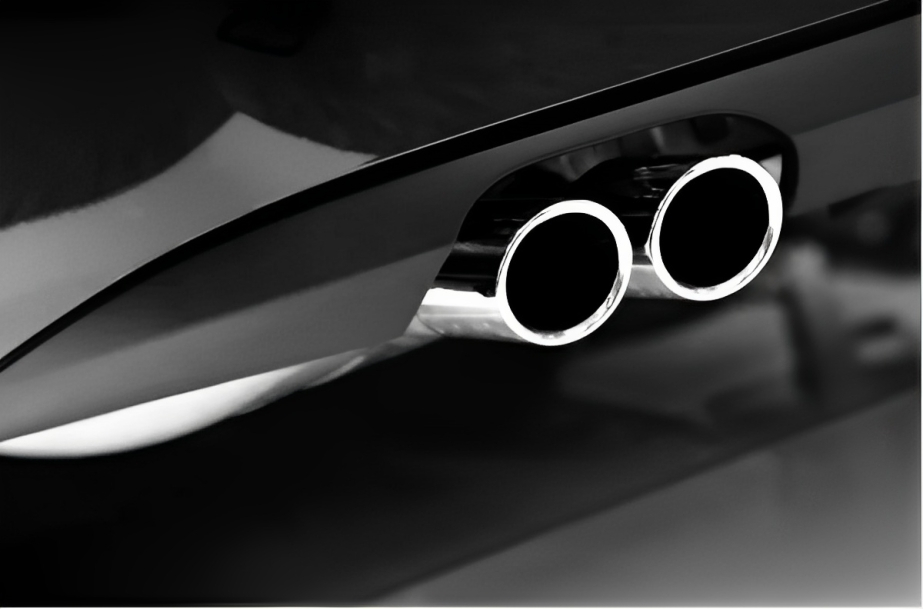
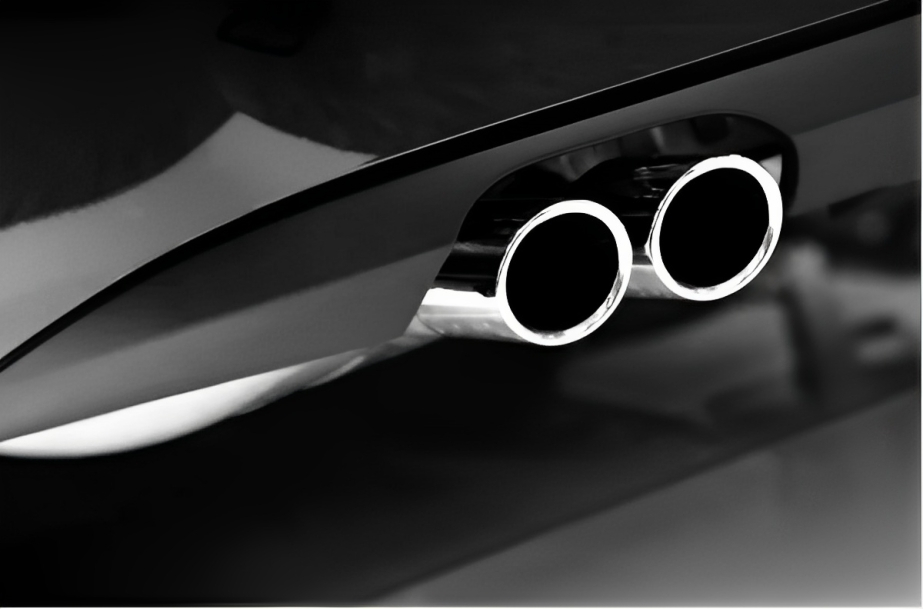