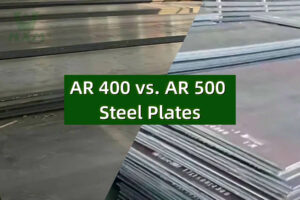
AR 400 vs. AR 500 Steel Plates
AR (Abrasion-Resistant) steel plates, specifically AR 400 and AR 500, are widely used in industries where durability and resistance to wear are essential. These plates are designed to withstand harsh conditions, offering high strength and excellent resistance to impact and abrasion. However, they differ in terms of hardness, applications, and specific use cases.