alloy steel vs carbon steel
In the vast realm of steel, both alloy steel and carbon steel emerge as pivotal players, each boasting unique characteristics that cater to diverse industrial applications. Understanding the nuanced distinctions between these two categories unveils a tapestry of properties, classifications, and application fields that shape their roles in the world of materials engineering.
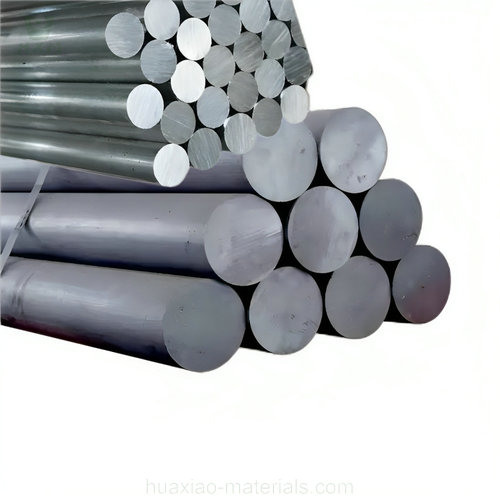
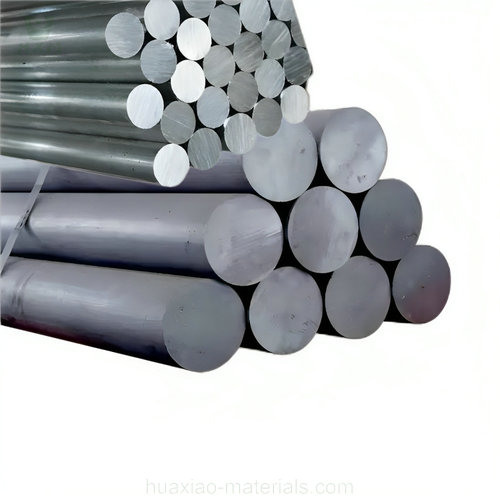