Tool Steel vs Carbon Steel
Tool steel contains alloying elements for durability and resistance to wear, ideal for tools and machinery. Carbon steel is primarily iron and carbon, chosen for general-purpose applications and affordability.
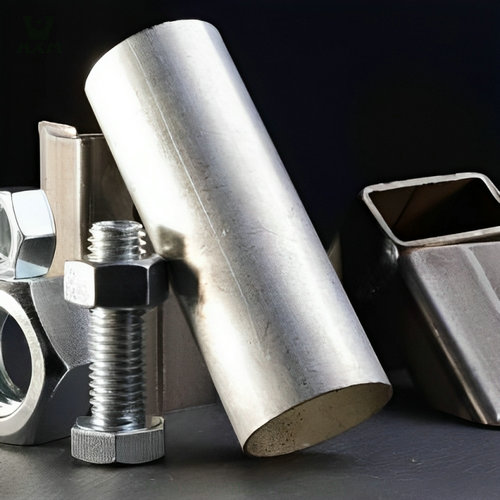
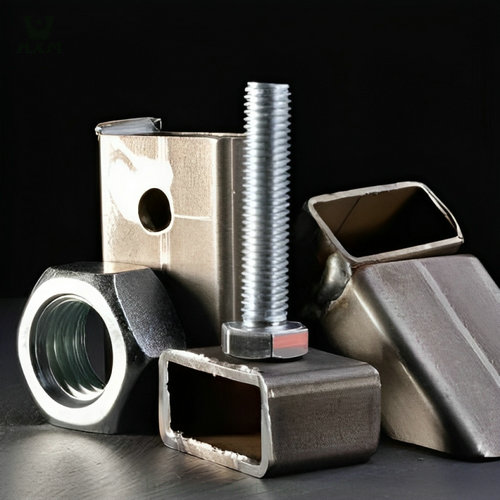
Tool steel contains alloying elements for durability and resistance to wear, ideal for tools and machinery. Carbon steel is primarily iron and carbon, chosen for general-purpose applications and affordability.
Tool steel and carbon steel are both essential materials used in various applications, but they have distinct differences in composition, properties, and applications. Here are the primary differences between the two:
In summary, tool steel and carbon steel serve different purposes and are chosen based on the specific requirements of a given application. Tool steel excels in specialized, high-performance applications where hardness, wear resistance, and heat resistance are critical, while carbon steel offers versatility and affordability for a wide range of applications.
Tool steel and carbon steel differ significantly in terms of hardness and durability due to their distinct compositions and intended applications:
In summary, tool steel excels in terms of hardness and durability, making it the preferred choice for applications where maintaining sharp edges, withstanding wear, and resisting deformation are crucial. Carbon steel, while versatile, is generally softer and less durable, making it suitable for applications that do not require the extreme hardness and wear resistance of tool steel.
The choice between tool steel and carbon steel for specific tool and blade applications depends on the requirements and demands of the application. Here are some general guidelines for when each type is preferred:
In summary, if the primary requirements are hardness, wear resistance, and the ability to withstand harsh conditions, tool steel is the preferred choice. On the other hand, if ease of sharpening and cost-effectiveness are more important, carbon steel is a suitable option, especially for knife and blade applications where sharpness and ease of maintenance are paramount. Ultimately, the choice should align with the specific needs of the tool or blade in its intended application.
Tool steel and carbon steel differ significantly in terms of their corrosion resistance due to differences in their composition and intended use:
In summary, neither tool steel nor carbon steel offers significant inherent corrosion resistance, and both can corrode when exposed to moisture and corrosive environments. Protection measures such as coatings, proper storage, and maintenance are essential to mitigate corrosion risk. If corrosion resistance is a critical requirement for a specific application, stainless steel or other corrosion-resistant alloys would be more suitable choices.
There are significant variations in cost between tool steel and carbon steel due to differences in composition, manufacturing processes, and intended applications:
In summary, tool steel is more expensive than carbon steel because it is engineered to have specific properties that make it suitable for demanding applications. Carbon steel, on the other hand, is more affordable and is used in a wide range of applications where the need for extreme hardness and wear resistance is less critical. The choice between the two depends on the specific requirements and budget constraints of the application.
Sharpening and maintaining tools and blades made from tool steel or carbon steel require different considerations due to their distinct characteristics. Here are some key points for each:
Sharpening Frequency: Tools and blades made from tool steel tend to have excellent edge retention and can stay sharp for extended periods. However, when they do require sharpening, it’s important to use appropriate sharpening methods and tools.
Sharpening Methods: Tool steel can be sharpened using abrasive sharpening stones, honing guides, and specialized sharpening systems. Diamond sharpening stones are particularly effective for maintaining the sharpness of tool steel.
Angle Control: Pay attention to the sharpening angle, which can vary depending on the tool or blade. Use a consistent angle for sharpening to achieve a uniform edge.
Coolant: When sharpening tool steel, especially high-speed steel (HSS), consider using a coolant or lubricant to prevent overheating and maintain the temper of the steel.
Maintenance: After sharpening, clean the blade or tool, and apply a thin layer of protective oil to prevent corrosion. Proper storage in a dry environment is essential to keep tool steel tools in good condition.
Sharpening Frequency: Carbon steel blades often require more frequent sharpening compared to tool steel. They may lose their edge faster but can be sharpened relatively easily.
Sharpening Methods: Carbon steel blades can be sharpened using various methods, including sharpening stones, honing rods, and sharpening machines. Whetstones are commonly used for maintaining carbon steel edges.
Angle Control: As with tool steel, maintain a consistent sharpening angle for carbon steel blades. The angle may vary depending on the intended use.
Rust Prevention: Carbon steel is susceptible to corrosion, so it’s crucial to keep blades dry and clean after use. Applying a food-safe mineral oil or blade oil can help prevent rust.
Regular Maintenance: Regularly inspect and touch up the edge to maintain cutting performance. Avoid leaving carbon steel blades in damp environments, as this can accelerate corrosion.
In summary, both tool steel and carbon steel tools and blades require regular maintenance to ensure optimal performance and longevity. Tool steel tools tend to have longer edge retention but require precision in sharpening, while carbon steel blades may require more frequent sharpening but are generally easier to maintain. Proper care, including cleaning, drying, and storage, is essential to prevent corrosion and maintain the cutting edge.
When choosing a stainless steel manufacturer, there are several critical factors to consider to ensure you select the right supplier for your needs. Here are the key factors to keep in mind:
Quality and Reputation:
Material Expertise:
Customization Options:
Production Capacity:
Quality Control and Testing:
Cost and Pricing Structure:
Delivery and Logistics:
Technical Support and Expertise:
Environmental Responsibility:
Certifications and Compliance:
Customer References and Reviews:
Communication and Responsiveness:
Long-Term Partnership:
Location and Accessibility:
After-Sales Support:
By carefully evaluating these factors and conducting due diligence, you can choose a stainless steel manufacturer that aligns with your project’s requirements and quality standards.
Copyright@2023 Huaxiao Metal Corporation Limited . All rights are reserved
WhatsApp us
Feel free to contact us!
If you need our products, please leave us a message with the specific specifications and quantity through the window on the right!
Reply within 24 hours