300 vs 400 series stainless steel
The 300 series stainless steel (e.g., 304) offers excellent corrosion resistance, suitable for applications like food processing and construction. In contrast, the 400 series stainless steel (e.g., 410) has lower corrosion resistance and is primarily used in areas like cutlery and appliance manufacturing.
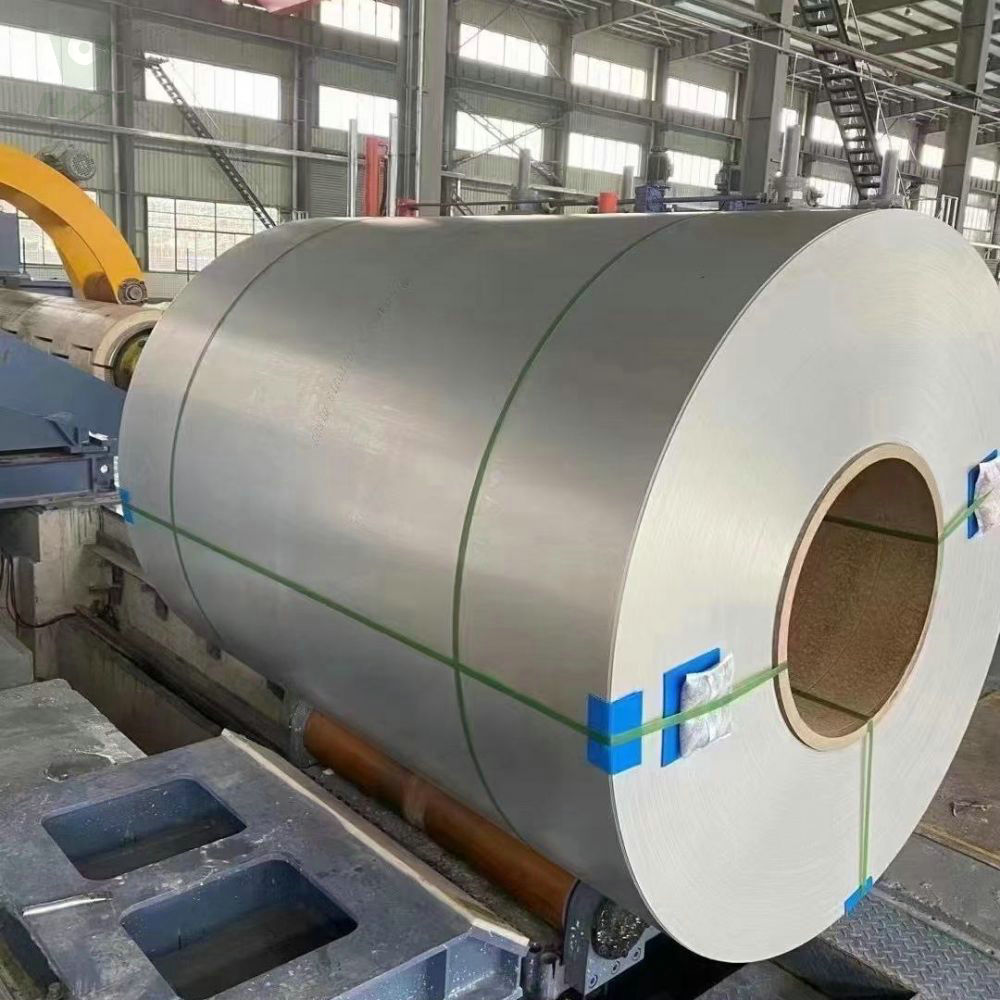
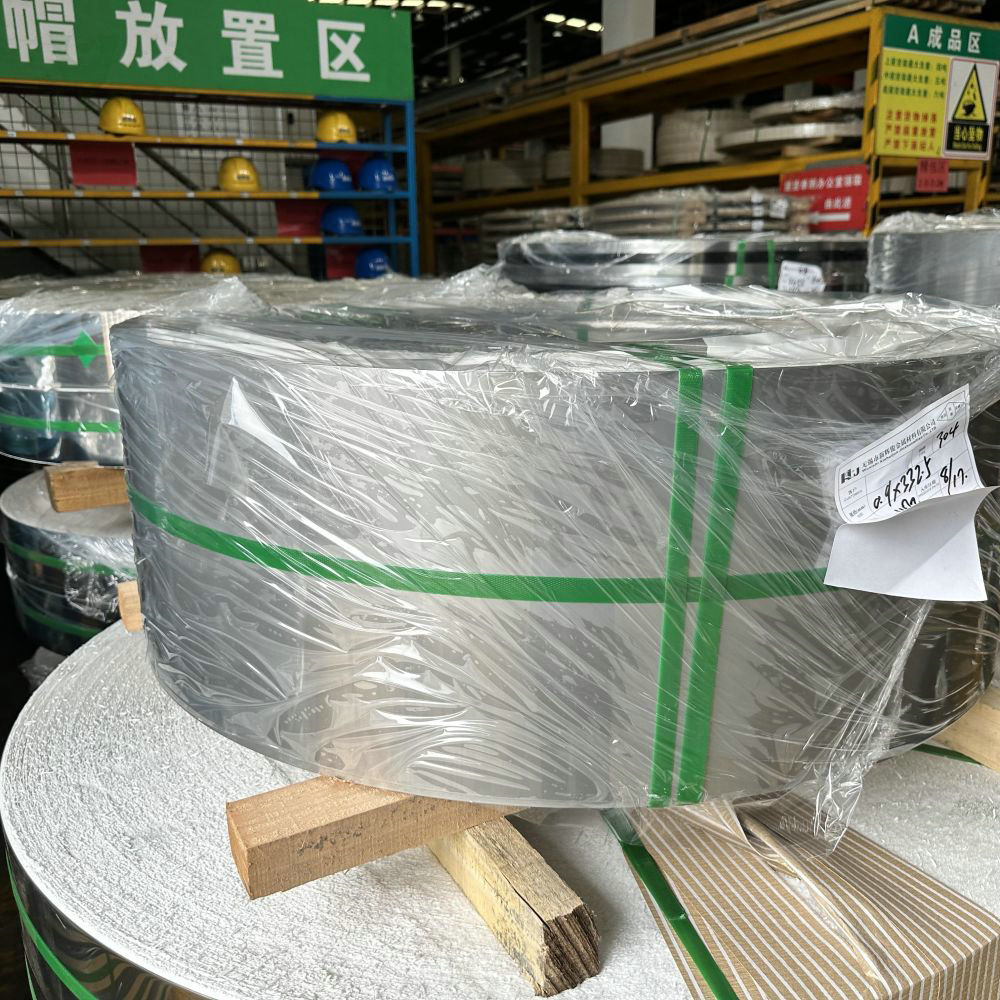