302 stainless steel
302 stainless steel is used in applications requiring high strength and corrosion resistance, such as springs, fasteners, and automotive components due to its durability and reliability.
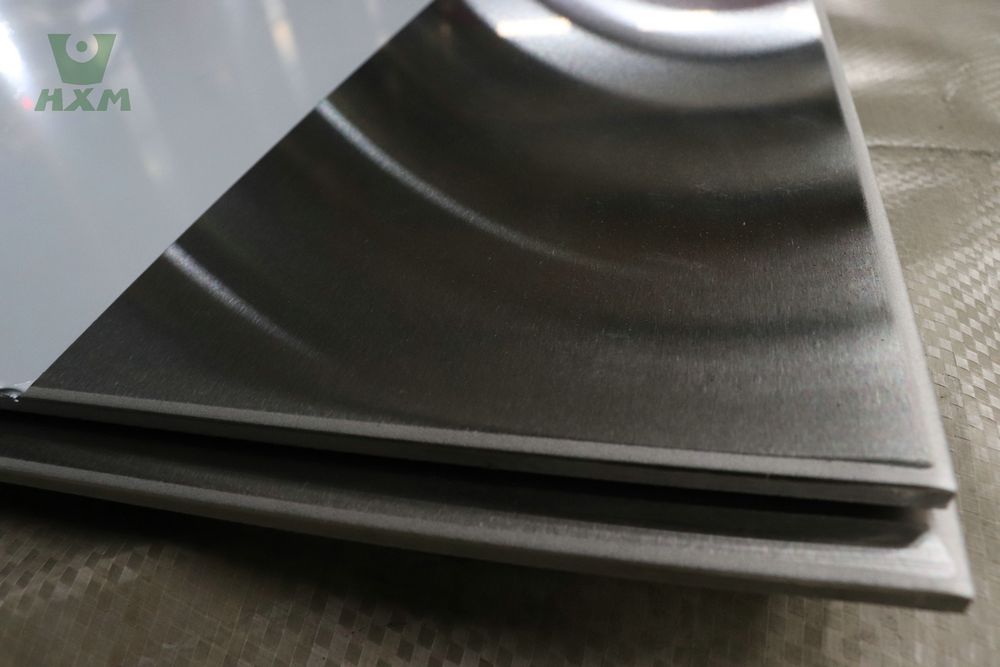
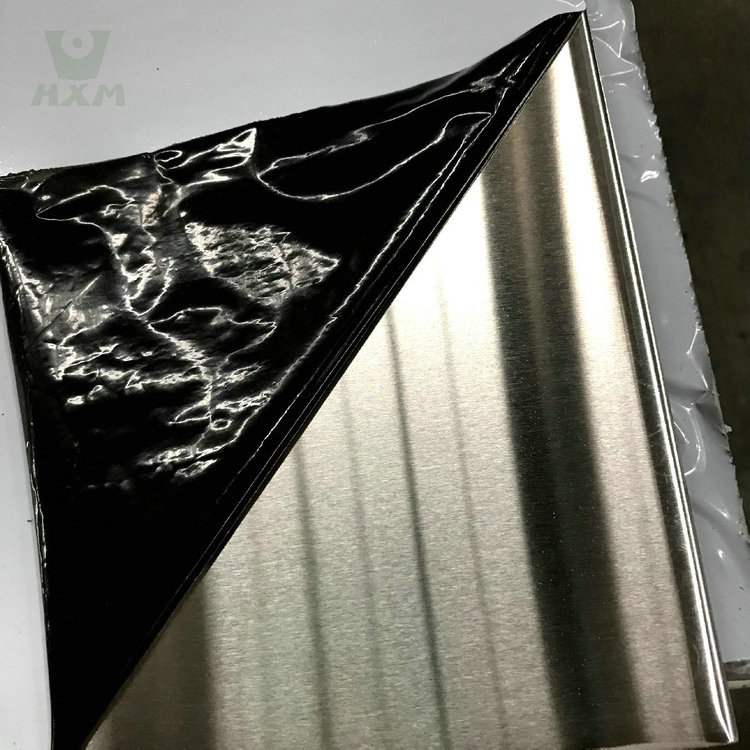
302 stainless steel is used in applications requiring high strength and corrosion resistance, such as springs, fasteners, and automotive components due to its durability and reliability.
302 stainless steel is a type of austenitic stainless steel known for its excellent corrosion resistance and high strength. It offers a combination of properties and characteristics that make it suitable for various applications. Here are the key properties and characteristics of 302 stainless steel:
Corrosion Resistance: 302 stainless steel exhibits outstanding resistance to corrosion, making it ideal for use in environments where exposure to moisture, chemicals, or corrosive substances is common.
Strength: It has good strength properties, allowing it to withstand heavy loads and high-stress conditions. This makes it suitable for structural components in various industries.
Ductility: 302 stainless steel is ductile, meaning it can be easily formed, bent, or stretched without breaking. This property is valuable for manufacturing processes that involve shaping and forming.
Machinability: It has good machinability, which means it can be machined, drilled, and cut with relative ease. This makes it suitable for precision machining applications.
Weldability: 302 stainless steel can be welded using various welding methods, including TIG and MIG welding, without significant issues. Proper welding techniques and filler materials are essential for successful welds.
Temperature Resistance: It maintains its mechanical properties and corrosion resistance at both high and low temperatures, making it suitable for applications in extreme temperature environments.
Non-Magnetic: 302 stainless steel is typically non-magnetic in the annealed condition, but it may become slightly magnetic after cold working. This property can be advantageous in certain applications.
Surface Finish: It can achieve a variety of surface finishes, including a polished, brushed, or satin finish, depending on the desired aesthetic and functional requirements.
Hygiene and Sanitary Properties: Due to its corrosion resistance and ease of cleaning, 302 stainless steel is commonly used in the food and beverage industry, as well as in medical and pharmaceutical applications where hygiene is crucial.
Cost-Effective: Compared to some other stainless steel grades, 302 stainless steel is often more cost-effective, making it a preferred choice for applications where a balance between cost and performance is required.
Applications: 302 stainless steel is used in various applications, including fasteners, springs, washers, wire forms, surgical instruments, automotive components, and more.
Austenitic Structure: It has an austenitic crystalline structure, which contributes to its corrosion resistance and overall durability.
It’s important to note that the specific properties and characteristics of 302 stainless steel can vary depending on factors such as the heat treatment, cold working, and the presence of alloying elements. Therefore, it’s essential to consider these factors when selecting 302 stainless steel for a particular application.
302 stainless steel finds applications in various industries due to its unique combination of properties. Some of the primary industries where 302 stainless steel is commonly used include:
Automotive Industry: 302 stainless steel is used in automotive applications such as fasteners, clamps, springs, and wire forms due to its strength, corrosion resistance, and durability.
Aerospace Industry: In aerospace, 302 stainless steel is employed for manufacturing aircraft components like springs, wire rope, and fasteners, where high strength and corrosion resistance are essential.
Medical and Healthcare: This stainless steel grade is used for producing surgical instruments, dental instruments, and medical devices because of its biocompatibility, corrosion resistance, and ease of sterilization.
Construction and Architecture: In construction and architectural applications, 302 stainless steel can be found in structural components, fasteners, and various fixtures, thanks to its corrosion resistance and aesthetic appeal.
Food and Beverage Processing: Due to its hygienic properties, 302 stainless steel is commonly used in food processing equipment, such as conveyor systems, storage tanks, and food handling machinery.
Marine Industry: For marine applications, 302 stainless steel is chosen for its resistance to saltwater corrosion, making it suitable for marine hardware, rigging, and boat accessories.
Manufacturing and Industrial Equipment: Manufacturers use 302 stainless steel in machinery components, springs, wire products, and various industrial equipment that require strength and corrosion resistance.
Chemical Processing: In chemical processing plants, 302 stainless steel is used for equipment and components that come into contact with corrosive chemicals, acids, and bases.
Electronics: This stainless steel grade can be found in electronic components, connectors, and small springs due to its electrical conductivity and corrosion resistance.
Renewable Energy: 302 stainless steel is used in wind turbines and solar panel installations for its durability and resistance to environmental factors.
Transportation: It can be found in transportation systems, including railways and buses, for manufacturing various components and parts.
General Manufacturing: 302 stainless steel is utilized in a wide range of manufacturing applications, including wire forms, fasteners, washers, and springs.
The versatility of 302 stainless steel makes it a preferred choice in these industries, where a balance between strength, corrosion resistance, and cost-effectiveness is required. However, the specific application and performance requirements will determine the suitability of 302 stainless steel in each case.
302 stainless steel offers good corrosion resistance in certain environments but may not be as corrosion-resistant as some other stainless steel grades, such as the austenitic 300 series. Here’s a comparison of the corrosion resistance of 302 stainless steel with other stainless steel grades:
302 Stainless Steel: It provides moderate corrosion resistance and is suitable for use in mildly corrosive environments. It may not perform well in highly corrosive or acidic conditions but is often used in applications where corrosion resistance is not the primary concern.
304 Stainless Steel: This austenitic stainless steel grade offers better corrosion resistance than 302 stainless steel. It is highly resistant to corrosion in most atmospheric, chemical, and freshwater environments. It is commonly used in applications where corrosion resistance is critical.
316 Stainless Steel: 316 stainless steel is known for its excellent corrosion resistance, especially in chloride-rich environments. It is highly resistant to pitting and crevice corrosion, making it suitable for marine, chemical, and coastal applications.
430 Stainless Steel: In comparison, 430 stainless steel is less corrosion-resistant than 302 and 304 grades. It is susceptible to rusting in moist and corrosive environments, especially when exposed to chlorides. It is often used in indoor applications or less demanding environments.
Duplex Stainless Steel: Duplex stainless steel grades, such as 2205 and 2507, offer superior corrosion resistance compared to 302 stainless steel, particularly in aggressive environments containing chlorides, acids, and high temperatures.
Ferritic Stainless Steel: Ferritic stainless steel grades like 409 and 430 provide moderate corrosion resistance and are commonly used in automotive exhaust systems and appliances.
It’s important to choose the stainless steel grade that best matches the specific corrosion challenges of your application. Factors such as exposure to corrosive substances, temperature, humidity, and the presence of chlorides or acids will influence the selection of the appropriate stainless steel grade to ensure long-term durability and performance.
There are specific machining and welding considerations for 302 stainless steel:
Cutting Tools: Use high-speed steel (HSS) or carbide cutting tools for machining 302 stainless steel. These tools can withstand the work hardening that occurs during machining.
Cutting Speed: Lower cutting speeds are generally recommended to prevent overheating and work hardening. Experiment with different cutting speeds to find the optimal one for your specific machining operation.
Coolant: The use of a water-based coolant or cutting fluid can help dissipate heat and improve the surface finish of machined parts.
Chip Control: Proper chip control is essential to prevent built-up edge and ensure smooth machining. Use chip breakers or chip control inserts when possible.
Preheat: Preheating is generally not required for welding 302 stainless steel. However, it can be beneficial for thick sections or when welding in cold conditions.
Welding Process: Common welding processes for 302 stainless steel include TIG (Tungsten Inert Gas) welding and MIG (Metal Inert Gas) welding. TIG welding is often preferred for its precise control.
Filler Metal: Use filler metals compatible with 302 stainless steel, such as AWS A5.9 ER308 or ER308L for TIG welding. These filler metals provide good corrosion resistance and mechanical properties.
Welding Parameters: Adjust welding parameters, including current, voltage, and travel speed, to achieve proper bead formation and minimize the risk of heat-affected zone (HAZ) cracking.
Post-Weld Heat Treatment: In many cases, post-weld heat treatment is not required for 302 stainless steel. However, it may be beneficial for relieving residual stresses and improving corrosion resistance in certain applications.
Shielding Gas: Use an appropriate shielding gas, such as argon, to protect the weld from atmospheric contamination and prevent the formation of oxides.
Back Purging: In critical applications, consider using back purging to protect the backside of the weld from oxidation and ensure a clean, corrosion-resistant weld.
Always follow the manufacturer’s recommendations and consult with experienced welders or machining experts when working with 302 stainless steel to ensure the best results and maintain the material’s properties and corrosion resistance.
302 stainless steel has temperature and environmental limitations that should be considered for various applications:
Corrosion Resistance: While 302 stainless steel offers good corrosion resistance in many environments, it may not be suitable for highly corrosive conditions, such as those involving strong acids or chlorides. In such cases, more corrosion-resistant stainless steel grades, like 316 or 316L, are recommended.
Exposure to Chlorides: 302 stainless steel can be susceptible to chloride-induced stress corrosion cracking (SCC) in the presence of chlorides, such as those found in saltwater or certain industrial environments. It is important to assess the specific chloride exposure and consider alternative materials when dealing with such conditions.
Exposure to Sulfuric Acid: 302 stainless steel may be vulnerable to attack in concentrated sulfuric acid solutions. Alternative materials like 316 stainless steel or specialty alloys should be considered for applications involving sulfuric acid.
Exposure to Alkaline Environments: 302 stainless steel may perform well in mildly alkaline environments. However, prolonged exposure to highly alkaline solutions can lead to reduced corrosion resistance.
Environmental Stressors: The performance of 302 stainless steel may be influenced by factors such as humidity, pollution levels, and exposure to abrasive particles. Careful consideration should be given to the specific environmental conditions in which it will be used.
It’s essential to assess the temperature and environmental conditions of your application and select the appropriate stainless steel grade accordingly. For applications involving extreme temperatures or highly corrosive environments, consulting with materials engineers or corrosion specialists is advisable to ensure the material’s suitability and longevity.
When searching for a reliable supplier of 302 stainless steel, several factors should be considered to ensure you choose the right supplier for your specific needs:
By carefully assessing these factors and conducting due diligence, you can select a 302 stainless steel supplier that aligns with your project requirements and expectations.
Copyright@2023 Huaxiao Metal Corporation Limited . All rights are reserved
WhatsApp us
Feel free to contact us!
If you need our products, please leave us a message with the specific specifications and quantity through the window on the right!
Reply within 24 hours