410 stainless steel vs 304
410 stainless steel has higher strength and hardness, suitable for wear-resistant applications.
304 stainless steel offers better corrosion resistance and versatility for various environments and uses.
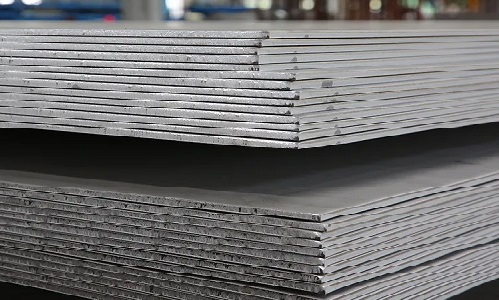
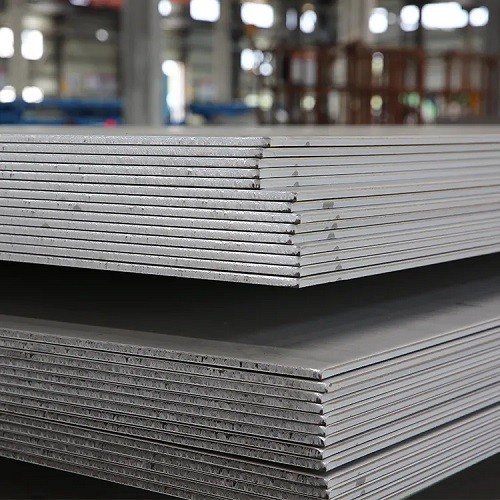
410 stainless steel has higher strength and hardness, suitable for wear-resistant applications.
304 stainless steel offers better corrosion resistance and versatility for various environments and uses.
The composition of 410 stainless steel differs from that of 304 stainless steel in terms of alloying elements, and these differences have significant impacts on their respective properties.
Chromium (Cr): 410 stainless steel contains a higher percentage of chromium compared to 304 stainless steel. Chromium is the primary alloying element that provides corrosion resistance to stainless steels. In 410 stainless steel, the higher chromium content contributes to its good corrosion resistance in mildly corrosive environments.
Carbon (C): 410 stainless steel contains a higher carbon content compared to 304 stainless steel. The elevated carbon content enables 410 stainless steel to be heat treated to achieve higher hardness and strength levels. This makes it a martensitic stainless steel with excellent mechanical properties.
Other Alloying Elements: 410 stainless steel may contain small amounts of other alloying elements like nickel and manganese, but these are typically present in lower concentrations compared to 304 stainless steel.
Corrosion Resistance: While both 410 and 304 stainless steels are stainless due to their chromium content, the higher chromium content in 304 provides better overall corrosion resistance, especially in harsh environments and when exposed to corrosive chemicals. 304 stainless steel is often used in applications where corrosion resistance is critical.
Mechanical Properties: The higher carbon content in 410 stainless steel allows it to be heat treated to achieve high levels of hardness and mechanical strength. This makes 410 stainless steel suitable for applications that require good wear resistance and moderate corrosion resistance. On the other hand, 304 stainless steel is not as hardenable through heat treatment and generally exhibits lower hardness and strength compared to 410.
Formability and Weldability: 304 stainless steel has better formability and weldability compared to 410 stainless steel. The higher carbon content in 410 can lead to increased susceptibility to cracking during welding, making it more challenging to work with.
Magnetism: 410 stainless steel is magnetic due to its martensitic structure, whereas 304 stainless steel is usually non-magnetic or only slightly magnetic due to its austenitic structure.
In summary, the differences in composition between 410 and 304 stainless steels result in distinct mechanical, corrosion resistance, and processing properties. The choice between the two depends on the specific requirements of the application, with 304 being favored for its corrosion resistance and 410 being chosen for its mechanical properties and wear resistance.
The magnetic behavior of stainless steels, including 410 and 304 stainless steel, is influenced by their crystal structures and alloying elements.
410 Stainless Steel:
304 Stainless Steel:
Effect on Applications Involving Magnetic Fields: The magnetic behavior of these stainless steels can have implications for their use in applications involving magnetic fields:
410 Stainless Steel: Due to its magnetic properties, 410 stainless steel can be attracted to magnets and may be influenced by magnetic fields. In some cases, this property can be advantageous. For example, 410 stainless steel can be used in applications where its magnetic response is useful, such as in components for magnetic locks, certain electrical devices, and sensors.
304 Stainless Steel: The non-magnetic or weakly magnetic nature of 304 stainless steel makes it suitable for applications where magnetic interference is a concern. In industries like electronics, aerospace, and medical devices, where magnetic fields can affect performance or measurements, the non-magnetic properties of 304 stainless steel can be beneficial.
In summary, the crystal structure and alloying elements in stainless steels like 410 and 304 contribute to their magnetic behavior. This magnetic property is considered when selecting the appropriate stainless steel grade for applications involving magnetic fields, ensuring that the steel’s behavior aligns with the specific requirements of the application.
Automotive Industry: 410 stainless steel is often used in automotive exhaust systems, where its higher strength and resistance to high-temperature oxidation are valuable. The exhaust components are subjected to elevated temperatures and mechanical stresses, making 410 a suitable choice.
Cutlery and Tools: Due to its excellent wear resistance, 410 stainless steel is commonly used in cutlery, knives, and surgical instruments. Its ability to maintain a sharp edge and resist corrosion in these applications is crucial.
Industrial Equipment: 410 stainless steel’s strength and wear resistance make it suitable for industrial equipment parts, such as valves, pumps, and fittings, especially in environments with abrasive substances.
Aerospace: In aerospace applications where components need to withstand harsh conditions and mechanical stresses, 410 stainless steel may be chosen for its strength and resistance to high temperatures.
Food and Beverage Industry: 304 stainless steel’s corrosion resistance, along with its ease of cleaning and hygiene maintenance, makes it a preferred choice for food processing equipment, kitchen appliances, and restaurant fixtures.
Medical Devices: 304 stainless steel’s biocompatibility, corrosion resistance, and ease of sterilization make it suitable for medical instruments, implants, and equipment where interaction with the human body is involved.
Architectural and Decorative Applications: 304 stainless steel’s aesthetic appeal, corrosion resistance, and versatility make it popular for architectural accents, interior design elements, and decorative fixtures.
Chemical Processing: In applications where corrosion resistance is crucial, such as chemical processing equipment and storage tanks, 304 stainless steel is often chosen due to its ability to withstand a wide range of corrosive chemicals.
Ultimately, the choice between 410 and 304 stainless steel depends on the specific demands of the application. While 410 is favored for its higher strength and wear resistance in applications like automotive and cutlery, 304 is preferred for its corrosion resistance and formability in industries like food processing, medical, and architectural design.
The welding characteristics of 410 stainless steel differ from those of 304 stainless steel due to their distinct compositions and metallurgical behaviors. When joining these alloys using various welding methods, certain considerations are essential to achieve successful and high-quality welds:
410 Stainless Steel:
304 Stainless Steel:
Considerations for Both Alloys:
In summary, while both 410 and 304 stainless steels have their own welding challenges and considerations, the key is to understand the unique characteristics of each alloy and apply the appropriate welding techniques, preheating, filler metals, and post-weld treatments to achieve strong and durable welds. Consulting with experienced welders or metallurgists is advisable when working with these alloys.
When deciding between stainless steel grades like 410 and 304 for various industries, factors such as material cost and lifecycle maintenance costs can indeed play a significant role in the decision-making process. Let’s explore how these factors can influence decisions:
Material Cost:
410 Stainless Steel: 410 stainless steel tends to be less expensive than 304 stainless steel due to its lower nickel content. The cost savings can be appealing, especially in larger projects or when cost considerations are a primary concern.
304 Stainless Steel: While 304 stainless steel can be more expensive due to its higher nickel content, it often provides excellent value in terms of its corrosion resistance, versatility, and wide range of applications.
Lifecycle Maintenance Costs:
410 Stainless Steel: While 410 stainless steel offers good corrosion resistance and wear resistance, it may not have the same level of corrosion resistance as 304 stainless steel, particularly in aggressive environments. In applications where corrosion resistance is critical, ongoing maintenance costs associated with corrosion protection and replacement of components may be higher.
304 Stainless Steel: 304 stainless steel’s superior corrosion resistance makes it a preferred choice in applications exposed to corrosive environments, such as marine, chemical, and food processing industries. Choosing 304 stainless steel can result in lower lifecycle maintenance costs due to reduced need for corrosion prevention measures, inspections, and replacements.
Considerations:
Application Environment: The environmental conditions in which the stainless steel will be used are crucial. If the application involves exposure to corrosive agents or high humidity, the long-term benefits of 304 stainless steel’s corrosion resistance could outweigh the initial cost difference.
Expected Service Life: Consider the expected service life of the components made from these stainless steel grades. If the components need to perform reliably for an extended period without frequent replacement, the corrosion resistance and durability of 304 stainless steel might justify its higher initial cost.
Weight and Strength Requirements: In industries where weight and strength are crucial factors, 410 stainless steel’s higher strength-to-weight ratio might provide advantages. However, if the application also requires corrosion resistance, it’s important to weigh the cost and benefits.
Decision-Making: The decision ultimately depends on the specific requirements of the industry, application, and project. For applications where corrosion resistance is paramount, and where lifecycle maintenance costs can significantly impact the overall budget, the higher upfront cost of 304 stainless steel might be justified. On the other hand, if corrosion resistance is less critical and cost is a primary concern, 410 stainless steel could be a more economical choice.
It’s important to conduct a thorough cost-benefit analysis, taking into account not only the initial material cost but also the potential long-term expenses associated with maintenance, repairs, and replacements. Collaborating with engineers, materials experts, and financial professionals can help make a well-informed decision based on the specific needs of the project or industry.
Selecting the right stainless steel supplier is crucial to ensure the quality, reliability, and cost-effectiveness of your materials. Here are some key factors to consider when choosing stainless steel suppliers:
Material Quality and Certification:
Product Range and Availability:
Experience and Reputation:
Technical Support and Expertise:
Supply Chain and Lead Times:
Price and Cost Considerations:
Customization and Value-Added Services:
Quality Control and Testing:
Sustainability and Compliance:
Customer Support and Communication:
Long-Term Relationship:
References and Recommendations:
Remember that selecting a stainless steel supplier is an important decision that can impact your projects and products. Take the time to research and evaluate multiple options before making a commitment. It’s also a good idea to establish clear terms and expectations in terms of pricing, delivery schedules, and quality standards before entering into a partnership.
Copyright@2023 Huaxiao Metal Corporation Limited . All rights are reserved
WhatsApp us
Feel free to contact us!
If you need our products, please leave us a message with the specific specifications and quantity through the window on the right!
Reply within 24 hours