How to cut stainless steel pipes?
To cut stainless steel pipes, secure it, choose a suitable tool like a hacksaw or angle grinder, follow the marked line, and deburr the cut end for a smooth finish.
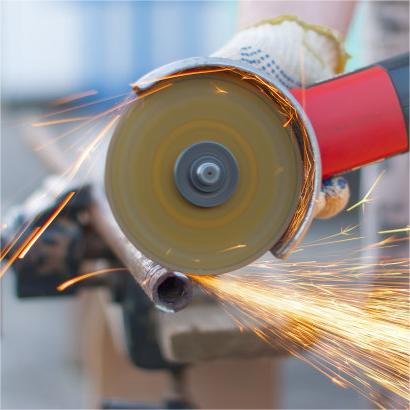
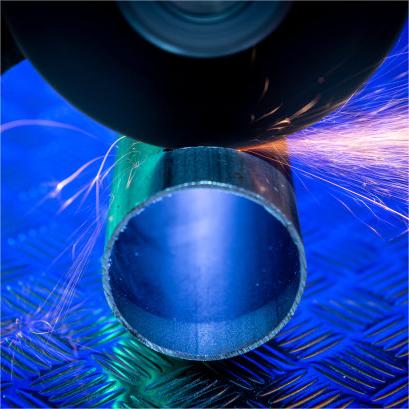
To cut stainless steel pipes, secure it, choose a suitable tool like a hacksaw or angle grinder, follow the marked line, and deburr the cut end for a smooth finish.
Selecting the appropriate cutting tool for stainless steel pipes is essential to ensure efficient and accurate cutting while minimizing tool wear and achieving a high-quality finish. Here are the primary factors to consider when you cut stainless steel pipes:
Material Hardness: Stainless steel is a hard material, and different grades can have varying levels of hardness. Choose cutting tools with the appropriate hardness and toughness to withstand the abrasion and heat generated during cutting without dulling or breaking.
Tool Material: High-speed steel (HSS) and carbide are commonly used tool materials for cutting stainless steel. Carbide tools offer greater hardness and wear resistance, making them suitable for cutting stainless steel. Consider using coated carbide tools for enhanced tool life and performance.
Tool Geometry: The tool geometry, including rake angle, clearance angle, and edge preparation, affects chip formation, cutting forces, and surface finish. Properly designed tool geometry can reduce cutting forces and heat generation, leading to improved tool life and surface quality.
Coolant and Lubrication: Stainless steel generates heat during cutting, which can lead to tool wear and workpiece distortion. Using an appropriate coolant or lubricant can help dissipate heat and reduce friction, leading to improved tool life and surface finish.
Cutting Speed and Feed Rate: Stainless steel requires lower cutting speeds and feed rates compared to softer materials. High cutting speeds can lead to excessive heat buildup and premature tool wear. Consult cutting speed and feed rate recommendations provided by tool manufacturers.
Cutting Depth: Adjust the cutting depth to avoid overloading the tool and workpiece, which can lead to poor surface finish, tool breakage, or workpiece distortion.
Vibration and Chatter: Stainless steel’s hardness can cause vibration and chatter during cutting, affecting surface finish and tool life. Choose tools with appropriate design features to minimize vibration, such as variable helix angles or anti-vibration designs.
Tool Coatings: Coated cutting tools, such as TiN, TiAlN, or TiCN, can provide improved wear resistance, reduced friction, and longer tool life when cutting stainless steel.
Tool Stability: Using a rigid and stable setup, including the machine tool, toolholder, and workholding, is crucial for achieving accurate cuts and avoiding chatter.
Surface Finish Requirements: Consider the required surface finish of the cut. Finer surface finishes may require specialized cutting inserts or tool geometries.
Machine Rigidity: Ensure that the machining equipment is rigid and well-maintained to avoid vibrations and achieve accurate cuts.
Tool Wear Monitoring: Some cutting tools come with wear monitoring features, such as inserts with wear indicators. Monitoring tool wear can help prevent premature tool failure and ensure consistent quality.
Tool Replacement Costs: Balancing the cost of cutting tools with their performance and tool life is important. High-quality tools may have higher upfront costs but can provide better overall value through extended tool life and improved efficiency.
Operator Skill: Proper operator training and expertise in using cutting tools for stainless steel can greatly influence the cutting process’s success.
Choosing the right cutting tool involves considering these factors in relation to the specific stainless steel grade, cutting conditions, and desired outcomes. Consulting with tool manufacturers or experts can help you make informed decisions and achieve optimal results in stainless steel pipe cutting applications.
Clamps are often necessary to secure stainless steel pipes during the cutting process in various scenarios to ensure safety, accuracy, and a consistent quality of cuts. Here are some scenarios where clamps are essential and how they contribute to accurate cuts:
Large Diameter Pipes: When cutting large diameter stainless steel pipes, the weight and size of the pipe can make it challenging to hold it in place manually. Clamps provide a secure grip on the pipe, preventing movement that could lead to inaccurate cuts or accidents.
Thin-Walled Pipes: Thin-walled stainless steel pipes are more susceptible to deformation and vibration during cutting. Clamping helps stabilize the pipe and minimizes vibration, resulting in cleaner and more accurate cuts.
Precise Lengths: In applications where precise pipe lengths are required, clamps ensure that the pipe remains steady and at the correct position throughout the cutting process. This prevents variations in length due to pipe movement.
Angular or Bevel Cuts: Clamping is crucial when making angled or beveled cuts on stainless steel pipes. Without proper clamping, the pipe might shift during cutting, leading to inaccurate angles or bevels.
Safety: Clamping provides a secure and controlled environment for the operator. It minimizes the risk of injuries caused by the pipe slipping, getting caught in the cutting tool, or the operator’s hands being too close to the cutting area.
Uniform Cuts: Clamps ensure that the pipe remains in a consistent position, resulting in uniform cuts along the length of the pipe. This is especially important in applications where multiple pipe pieces need to be joined together.
Reduced Vibration: Vibrations generated during cutting can negatively impact the cutting tool’s performance and the quality of the cut. Clamping helps dampen vibrations, leading to cleaner and more precise cuts.
Preventing Workpiece Distortion: Clamps help prevent distortion in thin-walled stainless steel pipes that can occur due to cutting forces and heat buildup. Distortion can lead to misaligned or uneven cuts.
Enhanced Accuracy: Clamps ensure that the pipe remains in a fixed position, allowing the cutting tool to maintain consistent contact with the workpiece. This contributes to accurate and repeatable cuts.
Multiple Cuts: When making multiple cuts on the same pipe to create various lengths or shapes, clamps help maintain the initial reference point, ensuring each subsequent cut is accurate and aligned.
Complex Shapes: For cutting complex shapes or patterns, clamps hold the stainless steel pipe in place according to the desired layout, preventing deviations and maintaining the intended design.
Uniform Surface Finish: Proper clamping prevents movement that could cause chatter or irregularities on the cut surface, resulting in a smoother and more uniform finish.
It’s important to use appropriate clamping devices designed for the specific pipe diameter, shape, and cutting process. Properly selected clamps, along with the correct cutting tool, cutting parameters, and operator expertise, contribute to achieving accurate and high-quality cuts in stainless steel pipes.
Ensuring the accuracy of the cut when using manual tools like a hacksaw or a pipe cutter for cutting stainless steel pipes requires careful setup, proper technique, and attention to detail. Here’s how you can achieve accurate cuts:
Remember that practice improves accuracy. If you’re new to cutting stainless steel pipes, consider practicing on scrap pieces to gain confidence and refine your technique before working on critical projects. Additionally, using quality tools and ensuring they are properly maintained will contribute to achieving accurate cuts.
Deburring the cut end of a stainless steel pipe is an essential step that involves removing any burrs, sharp edges, or rough surfaces created during the cutting process. This step contributes significantly to the overall quality of the cut and subsequent connections in the following ways:
Safety: Deburring eliminates sharp edges and burrs that can pose a safety hazard to those handling the pipe. Sharp edges can cause cuts or injuries, especially when assembling or installing the pipes.
Ease of Handling: Smooth, deburred edges make it easier to handle and transport the pipes without the risk of injuring hands or damaging other materials.
Sealing and Connection Quality: In applications where pipes are joined using fittings or connectors, a clean, deburred end ensures a proper fit and prevents damage to gaskets, seals, or O-rings. Rough edges or burrs can compromise the integrity of seals and gaskets, leading to leaks or improper connections.
Preventing Contamination: Rough edges can catch and trap debris, dirt, or particles that can lead to contamination of the fluid or gas passing through the pipe. Deburring prevents the accumulation of contaminants, enhancing the overall system cleanliness.
Aesthetics: A neatly deburred pipe end provides a professional and clean appearance, which is especially important in visible or architectural applications.
Flow Efficiency: Deburring the cut end ensures smooth internal surfaces, reducing turbulence and friction within the pipe, which can contribute to efficient fluid or gas flow.
Reduced Corrosion Risk: Burrs and rough edges can create crevices or stress points where corrosion can start. Removing these imperfections reduces the risk of localized corrosion and extends the pipe’s lifespan.
Tightening and Seating: When threaded connections are used, deburring helps the threads engage properly, ensuring smooth and effective tightening without undue stress on the threads.
Uniform Welding: In applications where pipes are welded, deburring ensures a clean and uniform welding surface, promoting better quality and strength of the weld joint.
Ease of Inspection: Deburred pipe ends are easier to inspect for quality, as burrs and rough edges can obscure imperfections or defects in the cut.
To deburr a stainless steel pipe, you can use various tools such as files, deburring tools, abrasive pads, or even sandpaper. The goal is to create a smooth, uniform, and clean edge that ensures a reliable and efficient connection or use in your application.
When guiding customers in choosing the right cutting method for their specific stainless steel pipe cutting requirements, you’ll need to consider several factors such as thickness, precision, available tools, budget, and project specifics. Here’s how you can help customers make informed decisions:
Pipe Thickness: The thickness of the stainless steel pipe is a crucial factor. Thicker pipes may require more robust cutting methods, while thinner pipes can be cut using a wider range of tools.
Precision Requirements: Depending on the application, customers might need precise cuts. Discuss the level of precision required and recommend methods that can achieve the desired accuracy.
Budget Constraints: Different cutting methods have varying costs associated with equipment, tools, and labor. Help customers balance their cutting requirements with their budget.
Available Tools and Equipment: Consider what tools or equipment the customer has access to. If they have certain tools already, it might influence the most feasible cutting method.
Type of Cut: Determine whether the customer needs straight cuts, angled cuts, or more complex shapes. Some methods are better suited for specific types of cuts.
Project Scale: The scale of the project can affect the choice of cutting method. Large-scale projects might require faster methods, while smaller projects might allow for more meticulous approaches.
Time Constraints: Some cutting methods are faster than others. If the project has tight deadlines, this could influence the choice of method.
Safety Considerations: Ensure the chosen cutting method is safe for the operator and the surrounding environment. Some methods generate sparks or require protective gear.
Post-Cut Processing: Consider whether the cut edge requires additional finishing or deburring. Some cutting methods result in cleaner edges than others.
Material Properties: Stainless steel has specific properties that can affect the cutting process. Discuss the stainless steel grade, hardness, and other material characteristics.
Expertise and Skill Level: Assess the customer’s familiarity with different cutting methods. Some methods might require specialized skills or training.
Future Use: If the customer anticipates using the same cutting method for future projects, consider the long-term practicality of the chosen method.
Based on these factors, you can provide customers with a range of cutting options and their pros and cons. Some potential cutting methods for stainless steel pipes include:
By discussing these options with the customer and understanding their specific needs, you can help them choose the most appropriate cutting method that aligns with their project requirements and constraints.
Selecting the right stainless steel pipes supplier is crucial to ensure the quality, reliability, and timely delivery of your materials. Here are the factors to consider when choosing stainless steel pipes suppliers:
By carefully evaluating these factors, you can select a stainless steel pipes supplier that aligns with your project needs, budget, and quality expectations, ultimately contributing to the success of your project.
Copyright@2023 Huaxiao Metal Corporation Limited . All rights are reserved
WhatsApp us
Feel free to contact us!
If you need our products, please leave us a message with the specific specifications and quantity through the window on the right!
Reply within 24 hours