Is silicon steel magnetic?
Yes, silicon steel is magnetic due to its crystalline structure and silicon content. It’s used in transformers and motors for its high permeability and low core loss characteristics.
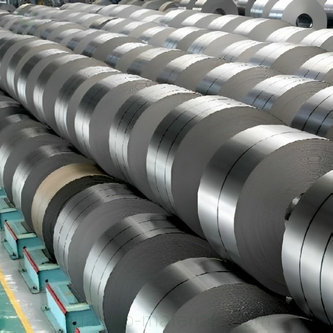
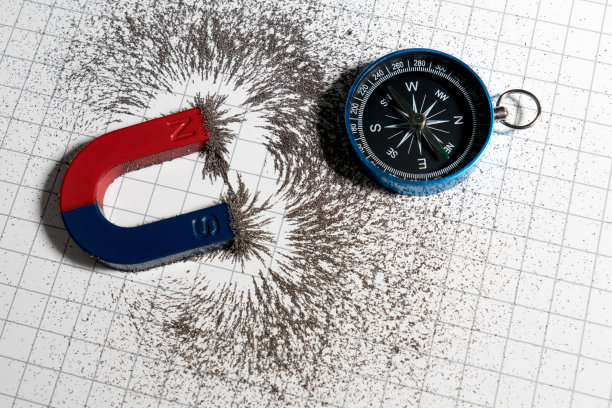
Yes, silicon steel is magnetic due to its crystalline structure and silicon content. It’s used in transformers and motors for its high permeability and low core loss characteristics.
Silicon steel, also known as electrical steel or transformer steel, is inherently magnetic due to its composition and crystal structure. It exhibits magnetic properties without the need for external magnetic fields. The magnetic behavior of silicon steel arises from its unique microstructure, which consists of very fine grains that are oriented in a specific direction.
In summary, silicon steel is naturally magnetic due to its unique composition and grain-oriented structure. Its magnetic properties make it an ideal material for applications requiring efficient magnetic coupling and low energy loss.
The presence of silicon in silicon steel plays a crucial role in influencing its magnetic properties, and silicon is chosen as an alloying element for specific reasons:
Reduced Core Loss: Silicon steel is used in applications that involve rapidly changing magnetic fields, such as in transformers and motors. The addition of silicon reduces core loss, which refers to the energy lost as heat in the material when subjected to alternating magnetic fields. This property is crucial for maintaining high energy efficiency in these devices.
High Magnetic Permeability: Silicon enhances the magnetic permeability of the steel, making it easier for magnetic flux to pass through the material. This property is essential for achieving efficient magnetic coupling in transformers and other electromagnetic devices.
Reduced Hysteresis Loss: Hysteresis loss is the energy dissipation that occurs when the magnetic domains within a material realign themselves as the magnetic field changes. The presence of silicon helps reduce hysteresis loss, further improving the energy efficiency of the material.
Grain Oriented Structure: Silicon facilitates the development of a grain-oriented microstructure in the steel. In this structure, the crystal grains are aligned in a preferred direction, enhancing the magnetic properties of the material.
Electrical Resistance: Silicon contributes to increased electrical resistance within the steel, reducing eddy current losses. Eddy currents are circular currents induced in a material by changing magnetic fields, and they can lead to energy loss.
Cost-Effectiveness: Silicon is abundant and relatively inexpensive, making it a practical choice as an alloying element in silicon steel production.
Compatibility with Manufacturing: Silicon can be alloyed with iron during the steelmaking process without significantly altering the properties of iron. This ease of alloying makes it feasible to produce silicon steel on an industrial scale.
In summary, the addition of silicon to silicon steel significantly improves its magnetic properties, including reduced core loss, increased magnetic permeability, and reduced hysteresis loss. Silicon is chosen for its ability to promote a grain-oriented structure, enhance electrical resistance, and improve overall energy efficiency in electromagnetic devices.
The orientation of crystal grains in silicon steel plays a pivotal role in its magnetic behavior and its efficiency in magnetic circuits. This unique grain orientation is a key feature of grain-oriented electrical steel, which is designed for high-performance applications in transformers, motors, and other electromagnetic devices. Here’s how grain orientation affects the magnetic properties and efficiency of silicon steel in magnetic circuits:
Directional Magnetic Properties: In grain-oriented electrical steel, the crystal grains are aligned in a preferred orientation, typically parallel to the rolling direction of the steel sheet. This alignment creates a pathway for the magnetic flux to follow in a specific direction, resulting in highly directional magnetic properties. This alignment reduces the resistance to the flow of magnetic flux through the material.
Enhanced Magnetic Permeability: The grain-oriented structure results in a significantly higher magnetic permeability in the direction of grain alignment. This means that the material allows magnetic flux to pass through it more easily along the preferred direction, resulting in improved magnetic coupling and efficiency in magnetic circuits.
Reduced Core Loss and Hysteresis Loss: The directional grain structure contributes to reduced core loss and hysteresis loss in grain-oriented silicon steel. This is because the aligned grains minimize the changes in magnetic domains during magnetization and demagnetization cycles, resulting in lower energy losses due to hysteresis and eddy currents.
Optimal Magnetic Flux Path: The grain-oriented structure creates a well-defined magnetic flux path within the material. This ensures that a higher proportion of the applied magnetic field is efficiently utilized to generate the desired magnetic output, contributing to the overall efficiency of devices like transformers and motors.
Efficiency in Magnetic Circuits: The grain-oriented structure enables silicon steel to efficiently transmit and transform magnetic energy within a circuit. This efficiency is essential in devices where magnetic circuits are involved, as it helps minimize energy losses and ensures accurate and reliable performance.
In essence, the orientation of crystal grains in silicon steel enables the material to exhibit superior magnetic properties, including high permeability and low energy losses. This directed alignment of grains optimizes the magnetic flux path, reduces losses, and enhances the efficiency of magnetic circuits, making grain-oriented silicon steel an ideal choice for applications that demand high performance and energy efficiency in electromagnetic devices.
Oriented silicon steel and non-oriented silicon steel are two distinct types of electrical steels with differing grain structures and magnetic properties. These differences arise from their manufacturing processes and intended applications. Here’s a comparison of oriented silicon steel and non-oriented silicon steel:
In summary, the choice between oriented and non-oriented silicon steel depends on the application’s specific magnetic requirements. The grain-oriented structure of oriented silicon steel provides better magnetic efficiency in a single direction, making it suitable for transformers. On the other hand, non-oriented silicon steel is versatile and used in various applications that require consistent magnetic properties regardless of flux direction.
The magnetic properties of silicon steel can be influenced by various factors over time. These factors can impact the efficiency and performance of electrical devices that utilize silicon steel cores, such as transformers and motors. Here are some specific factors and how they are managed in practical applications:
Temperature: Elevated temperatures can cause changes in the magnetic properties of silicon steel. Higher temperatures can increase core losses and decrease permeability. In practical applications, transformers and motors are designed with cooling systems to keep temperatures within acceptable ranges and prevent excessive degradation of magnetic properties.
Mechanical Stress: Mechanical stress can affect the alignment of crystal grains in silicon steel, potentially altering its magnetic properties. Transformers and other devices using silicon steel cores are designed to withstand mechanical stress and vibrations. Proper construction and insulation help minimize stress-related changes.
Time: Over extended periods, natural aging processes can lead to slight changes in the magnetic properties of silicon steel. Manufacturers account for these changes by using specific grades of silicon steel with stable properties over time.
Exposure to Magnetic Fields: Strong external magnetic fields can affect the magnetic properties of silicon steel. In practical applications, designers use shielding and proper core design to minimize the impact of external fields.
Chemical Composition and Processing: Variations in chemical composition and manufacturing processes can lead to differences in magnetic properties among different batches of silicon steel. Manufacturers closely monitor and control the composition and processing to ensure consistent magnetic behavior.
Surface Coatings: Surface coatings or insulation layers applied to silicon steel cores can affect magnetic properties. Careful selection of coatings and insulation materials is necessary to minimize any adverse effects.
Flux Density: Operating at high flux densities can saturate the silicon steel core, leading to increased losses and reduced efficiency. Designers select appropriate core materials and sizes to ensure optimal performance under expected operating conditions.
To manage these factors, engineers and designers in the electrical and electronics industries carefully consider the intended operating conditions of the devices using silicon steel cores. They select suitable grades of silicon steel with stable properties, design devices with proper cooling and shielding mechanisms, and perform thorough testing to ensure consistent magnetic behavior over time.
Additionally, ongoing research and development in materials science aim to improve the stability of silicon steel’s magnetic properties under various conditions, enhancing the efficiency and reliability of electrical devices.
When selecting silicon steel suppliers, several factors should be considered to ensure you receive high-quality materials that meet your specific requirements. Here are some key factors to keep in mind:
Quality and Certification: Choose suppliers who provide silicon steel that meets recognized industry standards and certifications, such as those from organizations like ASTM, IEC, or specific country standards. Look for suppliers with ISO or quality management system certifications to ensure consistent product quality.
Material Specifications: Ensure that the supplier offers silicon steel grades that align with your application requirements, including specific thicknesses, core loss characteristics, and magnetic properties.
Customization: If you have unique application needs, consider suppliers who can provide customized solutions, such as tailored material properties or sizes.
Reputation and Experience: Research the supplier’s reputation and industry experience. Established suppliers with a track record of providing reliable products and services are more likely to meet your expectations.
Supply Capacity: Evaluate the supplier’s capacity to provide the required quantity of silicon steel within your project timeline. Reliable suppliers should be able to meet your demand without causing delays.
Technical Support: Choose suppliers who offer technical support and assistance, especially if you have specific questions about material properties, applications, or processing.
Logistics and Delivery: Consider the supplier’s ability to handle shipping, delivery, and international logistics if necessary. On-time delivery is crucial to avoid project delays.
Cost and Pricing: While cost is a factor, focus on the overall value rather than solely on price. Cheaper options might compromise material quality and performance.
Testing and Quality Control: Inquire about the supplier’s testing procedures and quality control measures. Reputable suppliers conduct rigorous testing to ensure that their products meet specified standards.
Lead Times: Ask about lead times for both standard and custom orders. Suppliers who can provide shorter lead times may be more suitable for projects with tight schedules.
Environmental Compliance: Consider suppliers who follow environmentally responsible practices and provide materials that comply with relevant regulations.
References and Reviews: Request references from other customers who have used the supplier’s silicon steel products. Online reviews and testimonials can also provide insights into the supplier’s reliability and customer satisfaction.
Global Reach: If your project requires international distribution, choose suppliers with a global reach and experience in handling international shipments.
After-Sales Support: Inquire about the supplier’s after-sales support, warranty policies, and the ease of communication in case issues arise.
By carefully considering these factors and conducting thorough research, you can identify reputable silicon steel suppliers who can provide high-quality materials that align with your application’s requirements and quality standards.
Copyright@2023 Huaxiao Metal Corporation Limited . All rights are reserved
WhatsApp us
Feel free to contact us!
If you need our products, please leave us a message with the specific specifications and quantity through the window on the right!
Reply within 24 hours